Switch to Green Steel – It’s Not as Easy as It Sounds
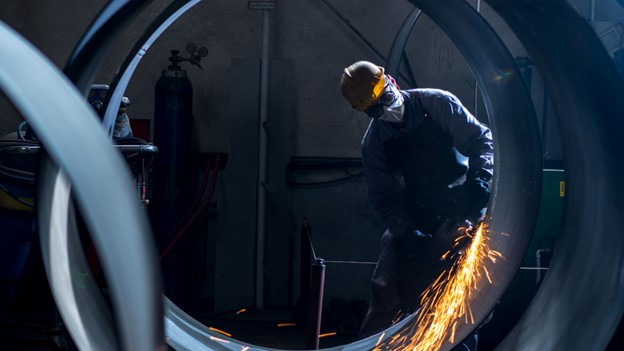
The US Department of Energy (DOE) announced as much as $6 billion in funding for 33 projects to decarbonize energy-intensive industries. Six of these projects involve the iron and steel industry, which accounts for $1.5 billion of federal investment. Undoubtedly, this funding and focus on decarbonization represent a significant step forward in the mission to reduce greenhouse gas emissions.
We know that implementing these changes requires transforming long-established processes that have been the foundation of the steel industry for many decades. Nevertheless, embracing this transformation becomes inevitable considering the escalating pace of global warming. The industry must adapt and find ways to navigate this daunting task, as transitioning to green steel is not only for the environment but also for the industry’s sustainability.
We understand that the transition to carbon-free steel production may seem like an overwhelming challenge. Luckily, we have all the resources to equip you when exploring alternatives, including access to business advisors with extensive manufacturing industry experience. But before you make that call, let’s go over the challenges you may face along the way and how you can potentially turn them into opportunities.
Carbon’s Role in Steel Production
Carbon’s role in steel production is crucial for several reasons. First, it plays a fundamental role in converting iron ore into steel. Carbon acts as a purifying agent, removing impurities from the iron to create a stronger and more durable final product.
Furthermore, the steel’s carbon content directly affects its properties. The presence of carbon influences the steel’s ductility, toughness, and weldability.
Evidently, carbon is so ingrained in your process that steel production may seem impossible without it. However, it’s important to consider environmental responsibility alongside the quality of your product. Steel production contributes to roughly 7% of global carbon dioxide emissions, and reducing this percentage could have a significant positive impact.
While carbon is essential, alternative approaches or methods could minimize or eliminate the industry’s carbon dependence. These include biomass use, absorption, adsorption, gas separation, and hydrogen-based steelmaking. These methods would require research before implementation. Consider your readiness in terms of budget, resources, workforce, and skills.
If these approaches prove too big of a leap considering your present circumstances, a practical starting point is scrap utilization. Steel is ubiquitous, present in our homes and buildings, and prominently used in construction. Unlike many other materials, steel retains its original properties even at the end of its life cycle. Consequently, you can recycle steel scraps to create new steel.
Implementation Challenges
To achieve low- and no-carbon steel production, the Department of Energy (DOE) has selected six projects for pilot demonstrations of transformative technologies. The focus is on hydrogen-steel production, electrolysis of iron ore, and carbon capture and utilization storage. However, implementing these technologies comes with several challenges that must be addressed for successful adoption.
One major challenge lies in adopting the hydrogen-based direct reduced iron (DRI) process. This approach produces steel with 0% carbon content. Although it offers a carbon-free solution, downstream processes often require a certain amount of carbon for steel manufacturing. Overcoming this challenge involves introducing the necessary carbon content without compromising the low-carbon aspect of the production method.
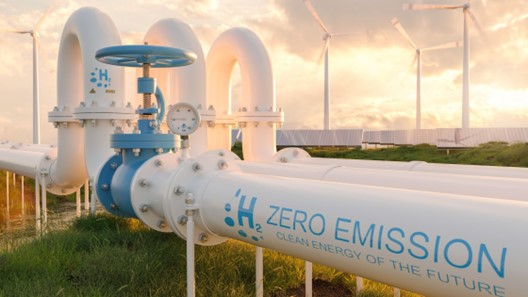
Another critical hurdle is ensuring a reliable supply of hydrogen. Producing hydrogen through electrolysis requires a substantial amount of electricity, raising concerns about the source and cost of electricity. Additionally, hydrogen storage, supply, and transportation require further exploration to optimize logistics and economics.
Producing steel by electrolyzing iron ore consumes a significant amount of energy. To ensure a low-carbon operation, it is imperative to source this electricity from renewable sources. However, securing a reliable and sustainable supply of renewable energy to power the process is another issue.
Scaling up the electrolysis of iron ore to meet commercial steel production demands poses another significant challenge. Developing the necessary infrastructure and technologies on a large scale while maintaining cost competitiveness requires substantial investments and careful planning.
Lastly, implementing carbon capture and storage (CCS) technologies can be financially demanding. The capture, transportation, and storage of CO2 generated in steel production require significant investments. Finding cost-effective solutions for CCS is crucial in making carbon-free steel production economically viable.
As we observe the outcome of the DOE’s pilot projects, it is important to recognize and address these implementation challenges. Overcoming these hurdles will pave the way for a sustainable and carbon-free future of steel production.
Turning Challenges into Opportunities
When faced with the inevitable, the only path forward is to make the best of the situation. Challenges always come with a flip side – opportunities. And we’re here to help you realize and make the most of them:
1. Technical Challenges
Developing and refining new processes to eliminate or reduce carbon emissions can be complex and costly. Thus, research and development efforts should focus on introducing necessary carbon content without compromising the low-carbon aspect of the production process. Additionally, scaling up technologies and infrastructure to meet production demands will require careful planning and substantial investments.
Opportunity: Addressing technical challenges can foster collaboration among industry stakeholders, technology providers, and research institutions. These partnerships can lead to knowledge sharing, joint research and development efforts, and resource pooling to overcome mutual challenges.
2. Cost Challenges
Alternative technologies being explored raise concerns about the cost of electricity, storage, supply, and transportation of hydrogen and the development of the necessary infrastructure and technologies.
Opportunity: Governments and organizations increasingly provide incentives and funding opportunities for companies that adopt low-carbon technologies and contribute to sustainable development goals. By successfully navigating the cost challenges, you can position yourself to access these incentives and funding options, which can significantly offset the initial investment costs and ensure a faster return on investment.
3. Supply Chain Challenges
The transition to carbon-free steel production may require changes in the entire supply chain. Ensuring a reliable supply chain of necessary resources, such as hydrogen and renewable energy for electrolysis, is essential.
Opportunity: Overcoming the supply chain challenges associated with carbon-free steel production can lead to the development of interconnected supply chain networks, from raw material suppliers to end-users, that support an efficient and effective value chain. This approach can ensure that all processes and stakeholders are aligned with the goal of producing carbon-free steel, resulting in reduced emissions and enhanced sustainability of the entire supply chain.
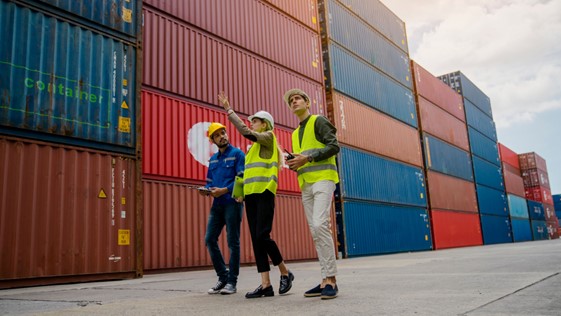
This is also an opportunity to leverage technological advancements in operations, logistics, and transportation to achieve greater efficiency and cost savings. For instance, companies can use predictive analytics, automation, and AI-powered technologies to optimize production and supply chain processes. This can result in more efficient resource use, reduced waste, and cost savings throughout their value chain.
4. Market Challenges
The shift towards carbon-free steel production presents market challenges that companies must navigate. These challenges include consumer demand for sustainable products, potential price differentials between traditional and low-carbon steel, and competition from companies still reliant on carbon-intensive processes.
Opportunity: By promoting the benefits of low-carbon steel and showcasing environmental responsibility, you can differentiate yourself in the market and tap into the growing number of eco-conscious consumers. Furthermore, you have the opportunity to forge partnerships with suppliers, customers, and industry organizations. Together, you can advocate for the broader adoption of low-carbon steel and drive policy changes that foster a more sustainable market.
It Can Be Easier – With Mutual Support and Collaboration
Acknowledging the challenges and potential difficulties in transforming your entire production process is essential to achieving a carbon-free future in the steel industry. It’s painful to look uphill when you’re alone. Yet, a transformation of this magnitude presents an opportunity for collaboration and mutual support among your peers in the steel industry. You can also rely on the incentives, grants, and resources offered by the government and other organizations that support the adoption of low-carbon technologies.
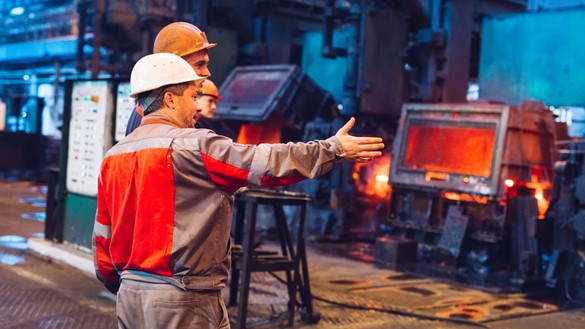
And hey, you have us! MBE CPAs offers business advice and guidance on financial protection to ensure you can successfully navigate this transformation and continue running your business without disruption. So, why not take advantage of our manufacturing specialization?